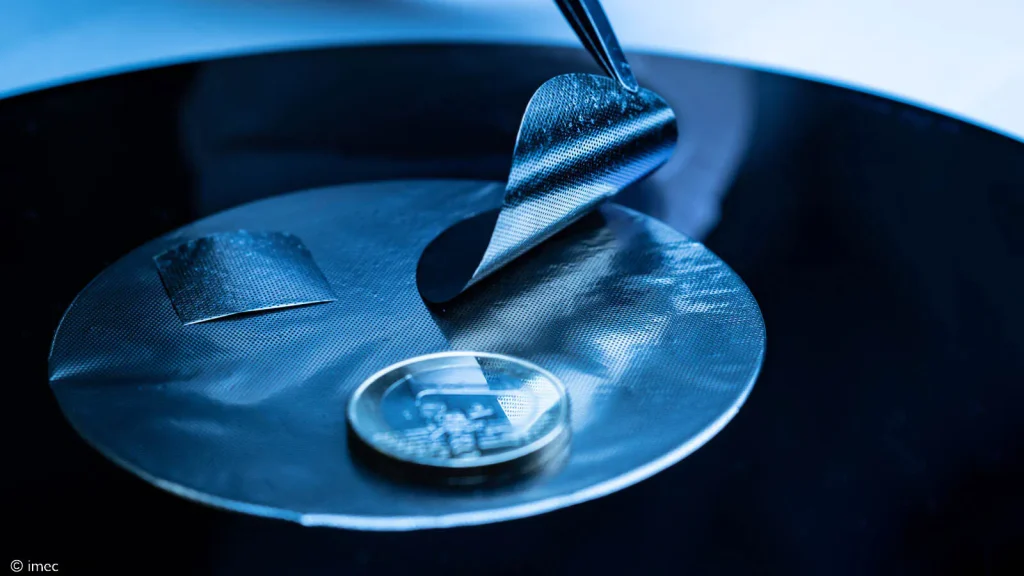
The researchers have developed a 3D structure made of interconnected nanowires, which can now be used as a freestanding electrode in electrochemical flow cells.
The results confirm that the use of these structures can yield a 100-fold increase in current density compared to conventional planar nickel electrodes.
Large-scale production of green hydrogen and green hydrocarbons becomes essential to decarbonize industries.
Today, two commercially available options exist for megawatt-scale hydrogen production: classical alkaline water electrolysis (AWE) and proton exchange membrane electrolysis (PEM).
However, both technologies face challenges that need to be overcome to further improve the competitiveness of large-scale production of green hydrogen.
Researchers from imec and KU Leuven developed a 3D structure of interconnected nanowires.
These nanomesh structures combine high porosity with an extremely high surface area, providing plenty of reaction sites.
Due to its unique material properties, nanomesh structures are attractive for numerous electrochemical applications, including electrolysis. They can be created via electroplating, an up-scalable fabrication flow, which makes them cheaper than currently used metal foams.
Until now, non-porous support substrates were needed to provide sufficient mechanical robustness to the highly porous nanomesh.
However, to exploit these compelling nano-architectures as freestanding electrodes in electrochemical flow cells, it is essential that the gaseous reagents and products can freely flow in and out.
Therefore, the nanowire networks must be supported by a porous structure that is accessible from all sides.
Researchers from imec now published their results on a monolithically integrated nickel nanomesh with an open support grid.
This improved nanomesh structure allows gaseous reagents and products to be introduced and removed efficiently from the reaction sites.
In an experimental setup they demonstrated that the theoretically available surface area of the nanomesh is almost completely available; resulting in a 100-fold current density increase compared to using conventional planar nickel electrodes.
The results confirm that the 3.5 micrometer thin nanomesh electrode has incredible potential in throughput and conversion rates.
“To achieve large-scale production of green hydrogen at offshore wind farms, where space is limited, we need to develop compact electrolysers with high efficiency,” said Bart Onsia, business development manager at imec. “These results are a promising step towards the development of new electrolysers components, and we are committed to continuing our research in this area to drive the transition to a more sustainable future.”
Philippe Vereecken, imec fellow and part-time professor at KU Leuven: “I am excited that we have been able to further enhance our nanomesh materials and demonstrate their potential in an industry-relevant setup. We have chosen nickel for the current demonstrations for hydrogen production, an area in which we partner with VITO within Hyve, a Belgian consortium that pursues cost-efficient and sustainable hydrogen production on gigawatt scale.”
“And the versatility of the nanomesh allows for a much wider portfolio of materials and applications. For instance, we can use copper or silver for CO2 reduction in gas diffusion electrodes,” says Nina Planckensteiner, Marie-Curie post-doctoral researcher at imec. “We are excited to continue exploring the potential of the nanomesh for a wide range of electrochemical applications.”